測定原理
【 概要 】
当社の金属接合部の非破壊非接触測定法は、金・銅・アルミの半導体ワイヤボンド・電子回路基板のハンダ付け・微小部位の溶接などの検査にご利用頂けますが、ここでは半導体製造後工程の金や銅の細径ワイヤボンディング接合検査に付いて、その測定原理を説明します。
一般的なIC(集積回路)の入出力信号をプリント回路基板と接続するには、IC回路とパッド(素子電極)、パッドとワイヤ、ワイヤとリードフレームなどの接合部を介在して構成され、その接合部は整流作用のない低抵抗なオーミック接触(接合)で有る事が必要となります。
接合部を構成するワイヤボンディングは、パッドとワイヤ間・ワイヤとリードフレーム間は金属同士の接合なので、通常は良好なオーミック接触となります。
ICのパッドはアルミ、リードフレームは酸化防止対策が施された銅などが多く、その間は金や銅の細径ワイヤで接続される事が多いです。しかし、同種金属同士の接合は良好にオーミック接触されますが、異種金属同士の拡散接合などは接合界面に熱伝導率の悪い合金層が生成され、電気伝導率も悪化します。
(金属の場合、熱伝導率と電気伝導率は比例関係です。)
現在、半導体製造工程におけるワイヤボンディングの品質管理方法として、フックなどによるプル強度測定法やシェア強度測定法が内外で規格化されていますが、細径ワイヤをプル強度測定するのは現実的に困難で、抜き取りによるシェア強度測定や接合面積測定による統計的品質管理が一般的と思われます。
また、簡易的な方法として画像処理によるワイヤループなどの外観検査も広く普及していますが、接合強度や電気伝導路性能などの測定は不可能と思われます。
その中で当社の非破壊非接触レーザーボンドテスターは、接合界面の伝熱量の差を瞬時に測定します。
レーザーボンドテスターの測定値は、接合部位の熱時定数と強い相関性があり、熱時定数が小さい接合部位は伝熱性(熱伝導率)が良好で、電気伝導率も良好です。
この様に、当社のレーザーボンドテスターはIC入出力のオーミック性(整流効果の無い低抵抗接続)を製造工程で評価する事ができ、ICの入出力毎の高速応答性や電力損失の個体差も選別することができます。
なお当社の測定方法は、規格化を進めています。
【 測定原理 】
本テスターの測定原理は、図1の様な金属接合構造の片方に熱エネルギーを加え、そのときの加熱波形と加熱部の温度応答波形の遅れ時間(熱時定数)が接合面積と強く相関するとの当社知見に基づいたものです。(特許取得済み)
また、電気抵抗率と熱伝導率の強相関関係から、電流が良く流れる接合(接合面積が広い)は、熱も良く流れ、その接合は一般的に強度も強いといえます。
図1の接合モデルに金属2の上方向から加熱すると、ある時間経過後、加熱量に比例した温度になります。このある時間を熱時定数(式1)といい、この熱時定数は熱容量と熱抵抗の積(式2)でも求める事ができます。
図1の物質を、熱等価回路法で図2の電気回路網に置換えると、熱容量はコンデンサー、熱抵抗は抵抗に置き換えることができ、コンデンサーと抵抗の並列回路として見ることができます。この電気回路の時定数も、コンデンサー容量と抵抗値の積(式3)で求める事ができます。
接合部の面積が広いと熱抵抗は小さく、狭いと熱抵抗が大きくなることから、接合面積が熱時定数に影響することが分かります。(式1、式2)
・熱時定数[s] =(比熱容量cp[J/kgK]×質量m[kg])/(伝熱係数h[J/㎡sK]×伝熱面積A[㎡])・・・(式1)=熱容量C[J/K]×熱抵抗Rt[K/W] ・・・(式2):Rt=1/hA
・回路時定数[s] =コンデンサー容量[F]×抵抗[Ω] ・・・(式3)
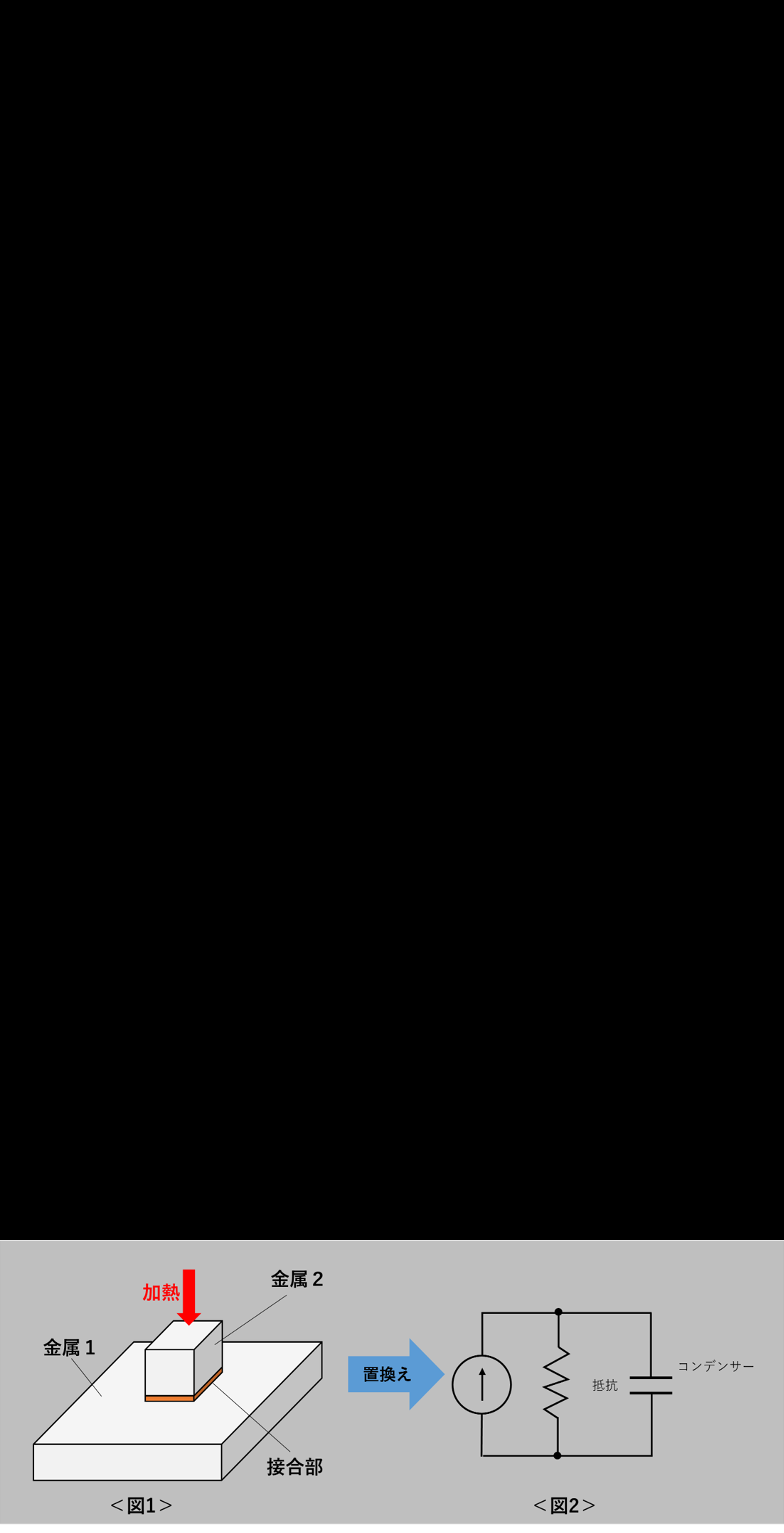
測定方法
熱時定数の測定方法は、インパルス(矩形波)加熱法が簡易的ですが、加熱点の温度応答測定の場合は、高分解能での測定が難しくなります。
当社は、正弦波変調したレーザー加熱波形と赤外放射温度応答波形を、位相検波(ロックインアンプ)することで位相差(≒時定数)を測定し、高分解能と安定性の高い測定を実現しています。(特許取得済み)
※)右図の位相は放熱構造に依存します。
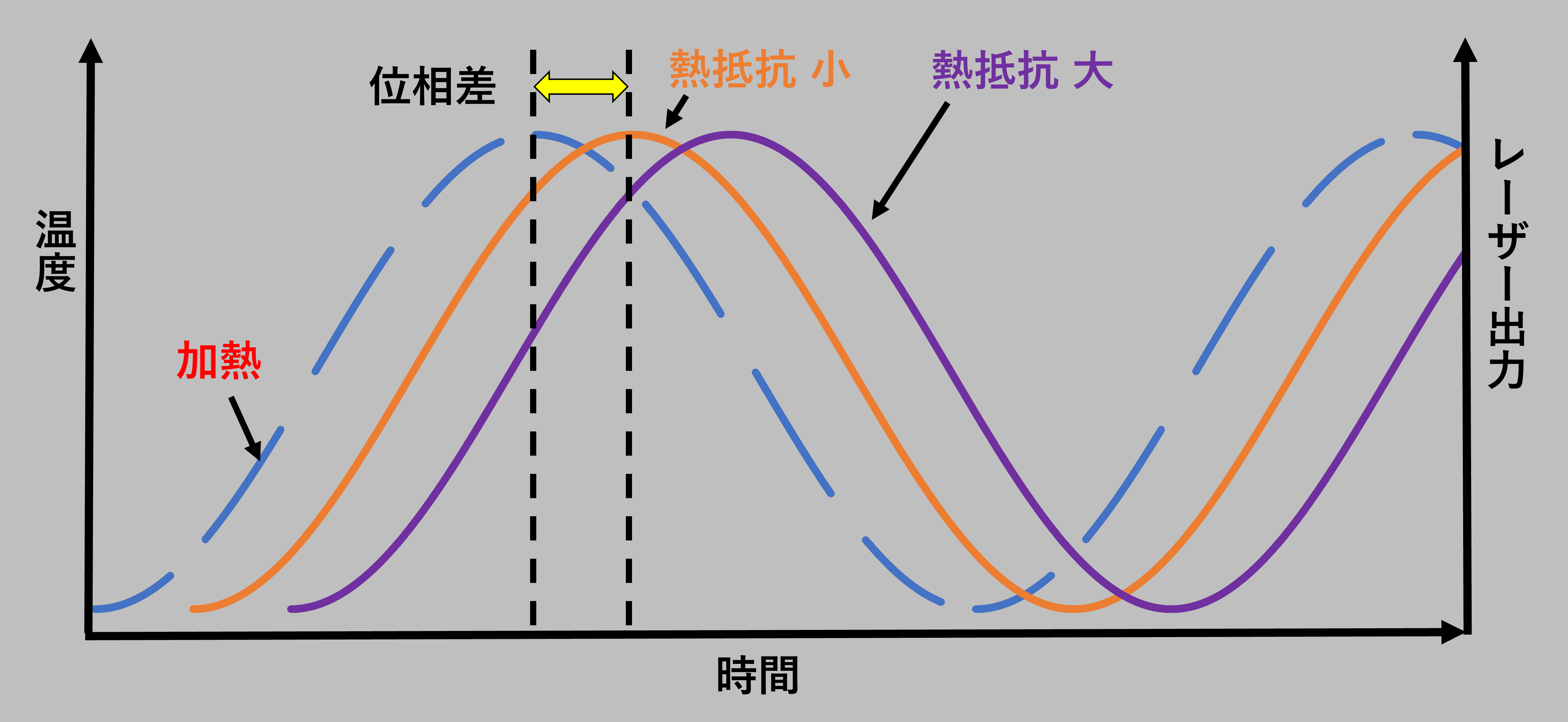
測定対象
標準的な測定対象は、パワー半導体製造後工程における太経アルミワイヤボンドです。
自動車・鉄道車両・産業機器・航空宇宙など高信頼性を要求される産業機器に使用されます。
金ワイヤボンド、銅ワイヤボンド、リードフレーム直付、バンプ、スポット溶接、ハンダ付けなどの非破壊・非接触の接合面積測定も可能です。別途ご相談ください。
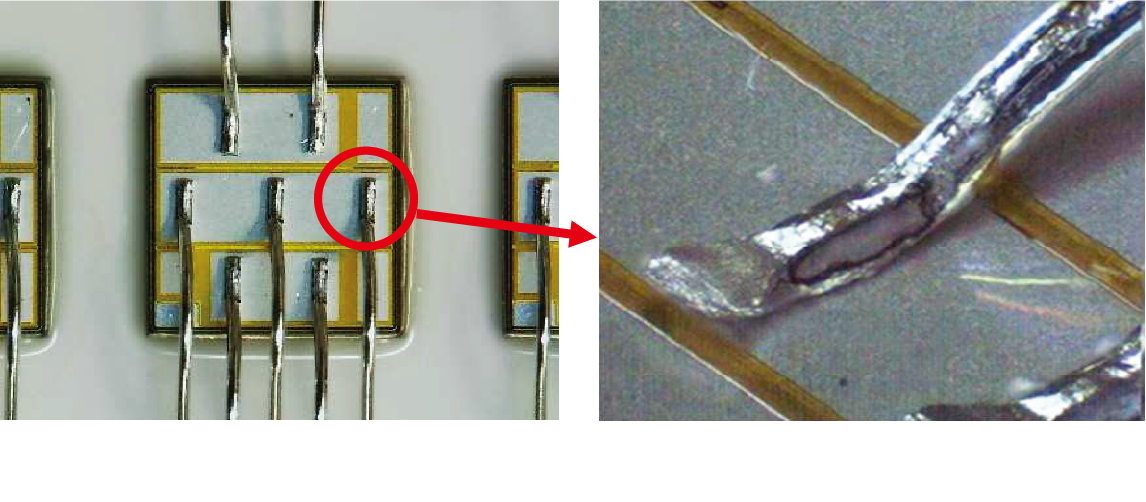
内部構造・動作イメージ
測定結果(Φ400μmアルミワイヤ)
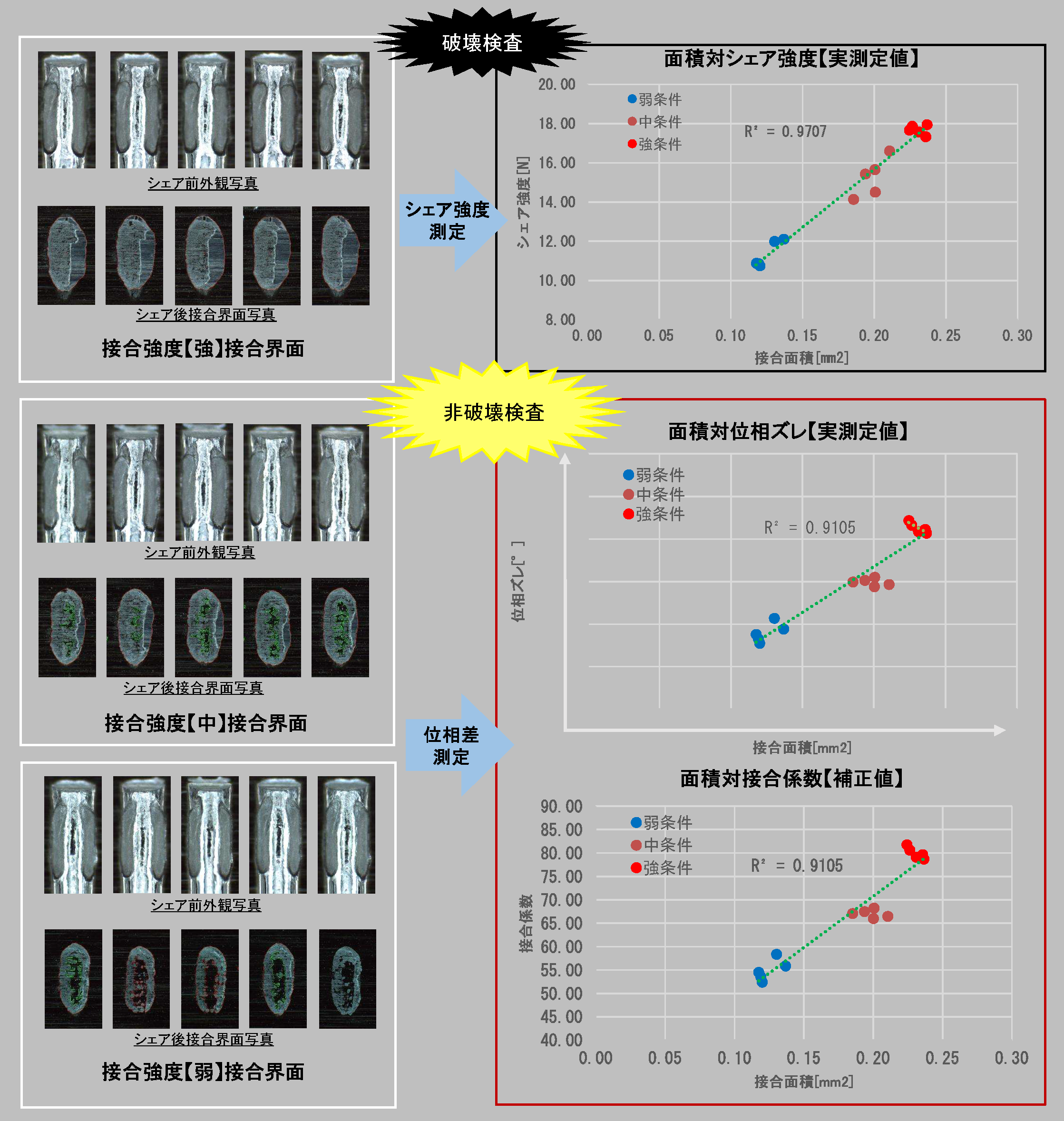